Best Practices in Warehouse Management for Freight Companies
Using a Warehouse Management System (WMS) can cut down manual work by up to 30%. This move towards automation shows how warehouse logistics are making tasks easier and reducing mistakes.
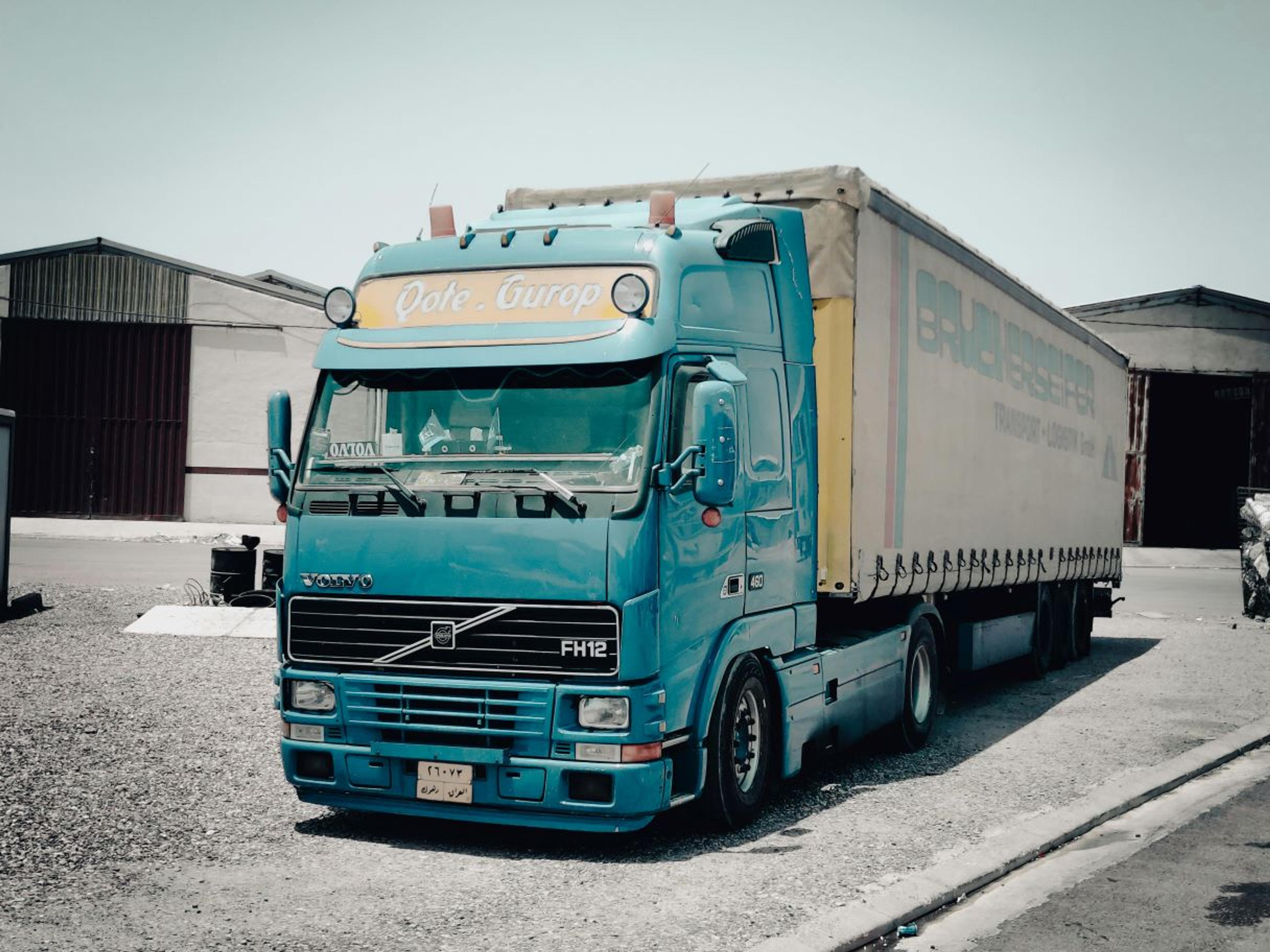
Understanding Warehouse Management Systems
To start well, balance your inventory and check how fast items move. This makes things easier to find and lowers costs. It also makes sure shipments go fast and keeps workers safe.
By focusing on warehouse logistics, companies build a solid base. Good planning, using data, and organized storage keep things running smoothly. This meets customer needs well.
Key Takeaways
- Adopt a WMS to reduce manual tasks and error rates.
- Review SKU velocity for optimal item placement.
- Keep inventory levels balanced to prevent slowdowns.
- Highlight worker safety through regular training.
- Rely on data analytics for fine-tuned operations.

Warehouse Management Systems help track stock levels and improve workflow. They make sure orders are accurate. This is done by monitoring things in real-time.
More companies are using WMS solutions. Almost 89% of them have adopted these tools. This can make tasks 20-40% more efficient and save up to 25% of space.
Definition and Purpose
A WMS is software that manages goods from start to finish. It keeps track of inventory quickly. This is why many in e-commerce and retail use it to handle costs and delivery times.
Key Features to Look For
Look for systems with:
- Real-time inventory tracking
- Integration with freight and shipping platforms
- Automated data capture through barcode or RFID
- Reporting tools for identifying inefficiencies
Performance Metric | Potential Improvement |
---|---|
Inventory Accuracy | Exceeds 99% |
Labor Efficiency | 20-40% Gain |
Space Utilization | 15-25% More Efficient |
Error Reduction | Up to 80% Decrease |
Importance of Efficient Layout and Design
A clear floor plan stops crowded aisles and saves space. Smart design cuts costs and boosts safety. Many freight companies save on labor by making spaces flexible.
Organizing racks, shelves, and paths makes more room. This helps businesses grow without moving.
Space Utilization Strategies
Going up is a smart way to add space without moving. Modular shelving and tall racks make room for more stock. This lets businesses grow with changing orders.
- Use stackable containers to maximize overhead areas
- Plan flexible sections to handle seasonally high volume
- Keep popular items closer to loading docks
Flow of Goods Considerations
Clear paths from receiving to dispatch help goods move faster. Shorter paths between picking and packing zones speed up orders. Good planning can increase throughput by 20%.
Layout Approach | Key Advantage | Potential Gains |
---|---|---|
Vertical Racking | Frees up ground space | 30% more storage capacity |
Clear Aisle Design | Reduces movement barriers | Up to 20% faster picking |
Inventory Management Techniques
Every freight operator wants to keep stock organized and orders filled quickly. Cycle counting helps keep inventory levels accurate. Reorder thresholds guide when to restock. Choosing the right storage for each item is key to smooth warehouse operations.
Barcoding and RFID systems make getting goods from dock to stock faster. This means customers get their orders quicker. A good warehouse management system tracks inventory down to the smallest detail. This ensures accurate billing and turnover rates.
Over time, this accuracy reduces mistakes and keeps shelves clear of old items.
ABC Analysis of Inventory
This method sorts stock by how fast it moves and its value. Fast-moving, high-value items are in Category A. Category B has items with moderate demand, and Category C has lower-priority items. Cycle counting keeps each category accurate, cutting down on errors and storage costs.
Just-In-Time Inventory Control
This method orders goods just when they're needed. It saves on storage costs and makes operations smoother. But, delays in production or transport can mess up this plan. So, having backup plans is important for good warehouse logistics.
Technique | Key Benefit | Potential Drawback |
---|---|---|
ABC Analysis | Focuses on high-value items | Less emphasis on slow-moving stocks |
JIT Control | Reduces holding costs | Vulnerable to supply chain delays |
Technology and Automation in Warehousing
AI-driven tools are changing how warehouses operate. Robots and automated systems are doing tasks that used to need human hands. This helps with the growing number of returns from online shopping.
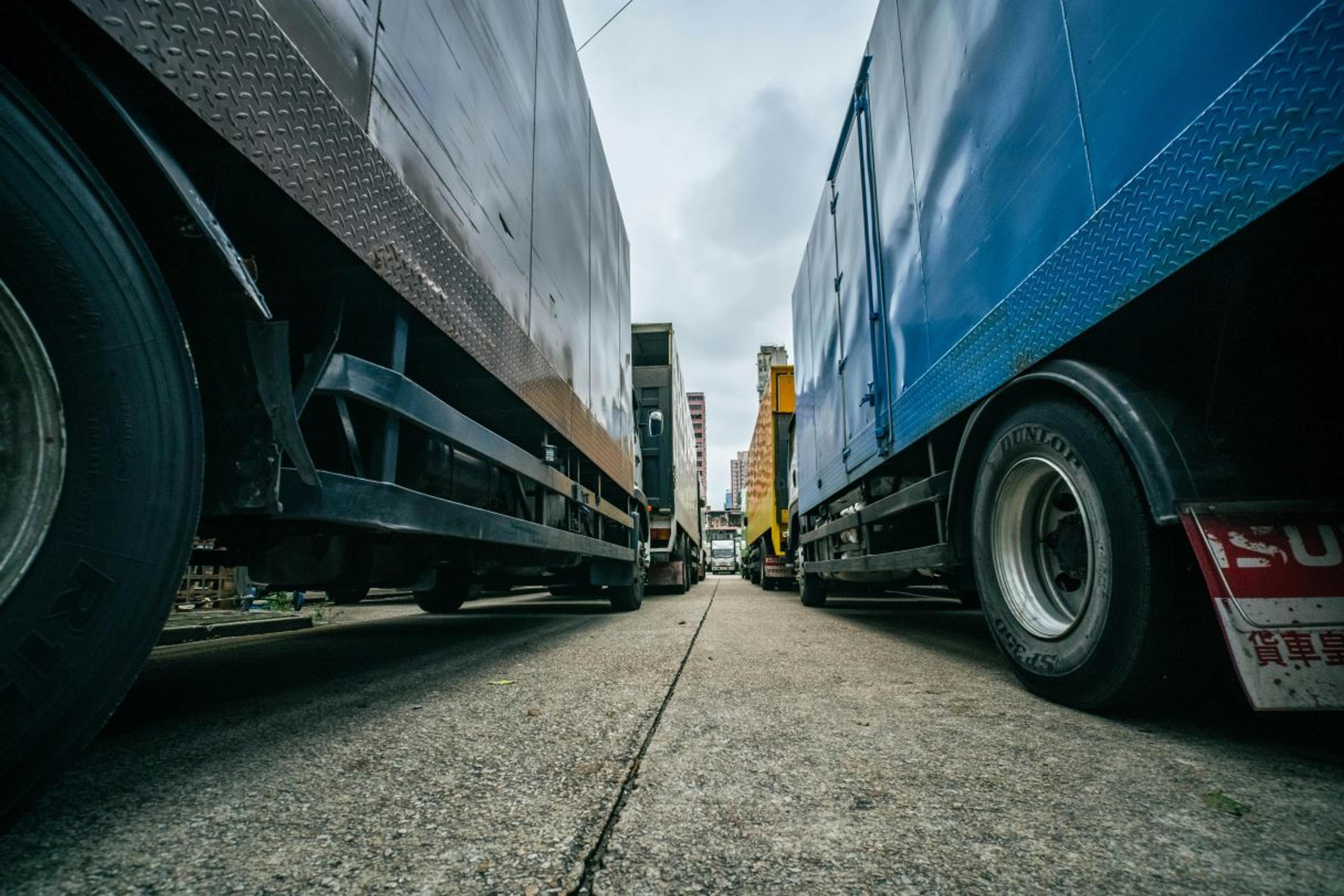
Benefits of Warehouse Robotics
Robots make tasks faster and more consistent, reducing mistakes. They work all day, moving goods without a break. This means better accuracy, faster delivery, and a safer workplace.
Software Solutions for Freight Management
Systems like Warehouse and Transportation Management Systems offer real-time data. They help manage routes, schedules, and inventory. This keeps goods moving and saves money.
Experts use this data to predict needs and plan better. This improves customer happiness and meets deadlines.
Effective Order Fulfillment Processes
The National Retail Federation says returns will hit $890 billion in 2024, up from $743 billion in 2023. This shows how key it is to ship orders quickly and correctly. Using smart picking methods and organizing storage well cuts down on time and errors.
Tools like pick-to-light or voice-assisted systems guide teams to the right spot. Fast items are placed near shipping areas to save steps. There are several ways to speed up picking, like batch or parallel picking.
Strategies for Rapid Order Processing
Warehouses get better by using smart picking plans. Batch picking is good for slower items, while parallel picking lets many workers pick at once. Pick and pass has products go through zones where each person focuses on certain items.
Packaging and Shipping Optimization
Good packaging cuts down on damage and postage costs. Many customers are willing to pay a 9.7% premium for eco-friendly choices. Using the right packing materials for each item reduces waste and keeps products safe. Organizing packing supplies well makes the end of order prep faster.
Picking Method | Use Case | Advantages |
---|---|---|
Pick and Pass | Items passing through defined zones | Reduces travel time |
Batch Picking | Collecting multiple orders at once | Improves efficiency for slow-moving SKUs |
Wave Picking | Coordinated scheduling for releases | Streamlines multi-shift operations |
Parallel Picking | Multiple workers assigned to one order | Boosts speed and productivity |
Workforce Management in the Warehouse
Strong teams are key to success. Experts say that well-trained workers and a safe place to work lead to better engagement and less turnover.
Managers who focus on training give their team the skills they need. This helps with equipment use, reduces mistakes, and boosts morale. Such efforts make warehouse operations smoother and more consistent.
Training and Development Programs
Continuous learning can improve order picking by up to 20%. Training on technology, lean methods, and teamwork keeps operations running smoothly.
- Onboarding helps new employees learn quickly.
- Cross-training expands skills to cover all needs.
- Annual refresher sessions update skills.
Employee Safety and Well-Being
Safe paths and ergonomic setups cut down on accidents and keep workers energized. Safe environments build trust, which boosts commitment in warehouse teams.
Program | Benefit | Potential Impact |
---|---|---|
Equipment Certification | Higher handling accuracy | Fewer damages and delays |
Safety Workshops | Reduced incidents | Stronger morale |
Wellness Initiatives | Improved well-being | Consistent performance |
Performance Metrics for Warehouse Operations
Measurable goals help logistics teams find areas to improve. They track metrics like order accuracy, pick rate, and labor costs. Inventory handling is key, as it impacts how quickly items move.
Top warehouses focus on customer happiness. They watch order accuracy, fulfillment speed, and turn rates. This quick feedback helps spot and fix issues.
Key Performance Indicators (KPIs)
Order accuracy shows how many orders are shipped right. Inventory turnover checks how often items are sold and replaced. These KPIs show if inventory handling is working well. They help decide if to grow storage or improve processes.
Quick analysis fixes problems before they hurt customer trust.
Analyzing and Improving Metrics
Leaders look at data to find patterns and change workflows. Small changes in picking or order time can make big differences. Using barcode scanning or voice-picking cuts down on mistakes.
Good scheduling keeps labor costs steady. Making changes based on data leads to lasting improvements in managing freight.
KPI | Formula | Benefit |
---|---|---|
Order Accuracy | (Correct Orders ÷ Total Orders) × 100 | Fewer Returns |
Inventory Turnover | Cost of Goods Sold ÷ Average Inventory | Stronger Demand |
Order Cycle Time | Ship Date − Order Date | Faster Fulfillment |
Capacity Utilization | (Used Space ÷ Total Space) × 100 | Reduced Costs |
Implementing Lean Warehousing Principles
Lean operations aim to make daily tasks smoother and remove unnecessary steps. Many businesses see big benefits when they add storage optimization to their daily routine. They often find their cycle times get better and errors go down over time.
Reducing Waste in Operations
More than 95% of companies that go lean report less waste. They work to get rid of extra items and make material handling faster. Regular checks help teams see how they're doing and make changes as needed.
- Eliminate duplicates and inactive items
- Streamline travel routes for quicker order collection
- Minimize holding large inventories to free up space
Continuous Improvement Strategies
Lean methods are all about making things better over and over. Companies that use just-in-time inventory can save up to 50% on holding costs. Regular checks of how employees work help make the warehouse more flexible as needs change.
Lean Practice | Key Outcome |
---|---|
Ongoing Audits | Uncovers inefficiencies for rapid correction |
Targeted Inventory Levels | Prevents space overuse and reduces clutter |
Timely Reassessments | Ensures continuous improvement and adaptability |
Enhancing Customer Satisfaction in Freight Services
Freight providers are under more pressure to offer smooth experiences. Giving timely updates and quick responses to questions builds trust. Using top-notch communication tools and real-time tracking helps strengthen client relationships.
Studies show that using automated warehouse solutions boosts satisfaction. This is because shipments are delivered on time and accurately.
Communication and Transparency
Customers want to know when their products will arrive. Keeping them informed and honest about delays can win their loyalty. Big carriers like UPS use tracking portals to show each step of a package's journey.
This clear information builds confidence and reduces worry.
Managing Customer Expectations
It's important to set realistic timelines and offer easy-to-reach support. Many freight companies match shipping times with what customers need. This way, surprises are few.
Good planning and watching over warehouse operations ensures shipments arrive as planned.
Sustainability Practices in Warehouse Management
Freight teams now have good reasons to go green. They can save on energy costs and meet customer demands. This move also improves how they handle inventory and boosts their brand image.
Starting with packaging is a smart first step. Using strong, recyclable materials at the loading dock helps avoid landfills. Reusable wraps also cut down on disposal costs and keep items safe during transport.
Eco-Friendly Packaging Solutions
Shipping companies gain from using materials that last longer and cost less to dispose of. Corrugated alternatives, compostable fillers, and biodegradable films reduce trash time. Many turn to reusable supplies to lessen environmental harm and streamline inventory management.
Energy Efficient Warehouse Operations
LED lights can cut energy use by over half. Solar panels offer tax benefits and stable energy prices. AR Racking’s ISO 50001 certification shows a worldwide push for less carbon. Electric vehicles and advanced dock levelers reduce emissions inside. Solar panels on large roofs can save money for big facilities over time.
Common Challenges in Freight Warehouse Management
Peak seasons bring sudden order surges, forcing teams to handle extra tasks. Mismanaged inventory can lead to stockouts in 20-30% of cases, hurting sales and customer satisfaction. Perishable goods often get lost, causing losses in food and beverage sectors.
It's key to keep a balanced workforce. Staff with skills in multiple areas can adjust to demand changes quickly. Cross-training helps manage spikes in volume, improving operational flow.
Identifying and Addressing Bottlenecks
Bottlenecks can cut efficiency and increase labor costs by up to 30%. Lack of visibility can hinder decision-making, leaving managers unaware of urgent tasks. Inaccurate forecasting can lead to wasted capacity or unfilled orders.
A systematic approach, along with storage optimization, can improve throughput. This helps manage operations better.
Adapting to Market Changes
E-commerce growth and changing trade rules require agile warehouse responses. Transportation costs rise by 10-15% yearly, adding pressure. Modern warehouses use data analytics and real-time tracking to improve layouts and stability.
The ability to adjust aisles, equip teams with new skills, and refine routes keeps businesses strong.
Challenge | Potential Impact | Mitigation Strategy |
---|---|---|
Seasonal Demand Surges | Excess labor costs | Cross-train staff |
Inaccurate Forecasting | Stockouts or overstock | Use real-time data |
Visibility Gaps | Delayed decisions | Deploy analytics tools |
Future Trends in Warehouse Management
E-commerce is changing warehouse logistics fast. Online orders are growing, needing flexible handling and precise tracking. Leaders say automated workflows boost order fulfillment by 15–20%.
Robotic arms improve accuracy by 30%, and collaborative robots increase efficiency by 25%. Soon, 70% of warehouses will use AI for quick decisions. This shift is towards cloud-based systems for better omnichannel fulfillment.
FAQ
Why are best practices in warehouse management essential for freight companies?
Good warehouse practices help with on-time deliveries and lower costs. They also keep safety standards high. By optimizing storage and handling inventory well, companies can improve their logistics and stay competitive.
How does a Warehouse Management System (WMS) improve inventory handling?
A WMS tracks products in real time and captures data automatically. It also provides clear reports. This technology cuts down on errors and works well with freight management, making inventory handling more accurate.
What layout strategies support storage optimization?
An efficient design focuses on product flow from start to finish. It uses every space well. Companies use vertical storage and automated systems for quick access to items, reducing travel time.
Which inventory management techniques are often recommended for warehouse logistics?
ABC analysis sorts inventory by how often it's used and its value. This lets teams focus on important items. Just-In-Time (JIT) inventory control matches order cycles with demand, cutting waste and costs.
What benefits do robotics and automation bring to warehouse operations?
Robots and automated systems do repetitive tasks, freeing staff for more important work. With software, companies like Amazon and DHL can reduce errors, speed up operations, and use resources better.
How can we improve order fulfillment speed and accuracy?
Using batch picking and pick-and-pass reduces travel. Good packaging protects items and lowers shipping costs. These methods improve storage and customer satisfaction.
Why is workforce management critical in a warehouse setting?
Training ensures employees follow lean principles and use equipment right. Safety training boosts morale and lowers injuries. This creates a better work environment and high standards.
Which KPIs should freight companies monitor for better performance?
Watch order accuracy, inventory turnover, and space use. Real-time tracking shows where to improve. This helps in handling inventory better, saving costs, and speeding up orders.
How does lean warehousing help with storage optimization?
Lean warehousing cuts waste in daily work. It organizes products to reduce travel, removes unnecessary steps, and improves processes. This makes companies adaptable and promotes growth.
What role does customer satisfaction play in warehouse logistics?
Happy customers come from clear communication, timely deliveries, and accurate tracking. Meeting these needs builds trust and encourages repeat business.
What sustainability practices benefit modern freight warehouses?
Using eco-friendly packaging, renewable energy, and energy-efficient lighting lessens environmental impact. These steps also cut costs and meet consumer demands for green logistics.
How do companies address peak demand periods or market shifts in warehouse operations?
Companies cross-train staff, scale up during busy times, and adjust workflows quickly. Being flexible helps maintain strong performance during e-commerce booms or changes.
What future trends should freight companies watch in warehouse management?
E-commerce growth demands advanced order systems and quick returns. Robotics, AI, drone deliveries, and analytics will shape warehouse logistics in the future.
--